《How to Choose the Right PVC Stabilizer for Wire & Cable》
Discover how to choose the right PVC stabilizer for wire and cable! This article provides an in-depth analysis of the characteristics, application scenarios and selection points of different types of PVC stabilizers to help you optimize product quality and production efficiency. Learn more about our professional selection guide now!
INDUSTRY NEWS
4/13/20254 min read
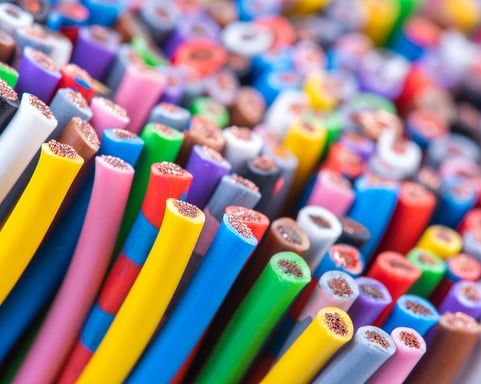
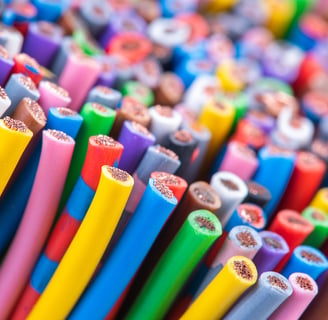
How to choose the right PVC stabilizer for wire and cable
Polyvinyl chloride (PVC) is a widely used insulation and sheathing material in wire and cable manufacturing. However, the performance of PVC depends greatly on the stabilizer selected. The right PVC stabilizer not only enhances the heat, weather and electrical properties of the product, but also optimizes production costs and environmental compliance. So, how to choose the most suitable PVC stabilizer for wire and cable? This article will provide you with a detailed selection guide covering key factors, stabilizer types and practical advice.
Why are PVC stabilizers critical for wire and cable?
PVC is susceptible to high temperatures, UV light and oxidation during processing and use, leading to degradation, discoloration or loss of performance. Stabilizers extend the life of PVC products by inhibiting these reactions. For wire and cable, the role of stabilizers is particularly important:
Heat resistance: Ensures that cables remain stable in high-temperature environments and prevents the insulation from deteriorating.
Electrical properties: Maintains the insulating properties of PVC and ensures the safe operation of cables.
Weather resistance: Enhance the cable's UV and oxidation resistance in outdoor environments.
Environmental compliance: meet RoHS, REACH and other regulatory requirements to reduce the use of hazardous substances.
Therefore, choosing the right PVC stabilizer is a key step to ensure the quality and market competitiveness of wire and cable.
Four key factors in selecting PVC stabilizers
When selecting PVC stabilizers for wire and cable, the following factors need to be focused on:
1. Cable application scenarios
Different types of wire and cable have different performance needs. For example:
Indoor cables: e.g. building cables, prioritizing cost-effectiveness and basic thermal stability.
Outdoor cables: e.g. power transmission lines, requiring excellent weathering and UV resistance.
High-temperature cables: e.g. automotive harnesses or industrial cables, requiring high heat resistance and long-term stability.
Defining the environment in which the cable is to be applied helps to filter out the most suitable type of stabilizer. For example, outdoor cables may require calcium-zinc stabilizers to enhance weathering resistance, while high-temperature cables may be more suited to organotin stabilizers.
2. Processing requirements
The choice of PVC stabilizers also needs to be matched to the process. Common wire and cable manufacturing processes include extrusion and injection molding, different stabilizers have different adaptability to processing temperature and shear:
Processing temperature: high temperature extrusion requires more heat resistant stabilizers.
Lubricity: Some stabilizers provide internal or external lubrication to reduce equipment wear and improve surface smoothness.
Flowability: High flowability stabilizers are suitable for complex molds or thin-walled cables.
When selecting, it is recommended to communicate with suppliers to test the performance of stabilizers under actual processing conditions.
3. Environmental and Regulatory Requirements
With the increasingly stringent global environmental regulations, the wire and cable industry is demanding more and more environmental performance from stabilizers:
Lead-free: Traditional lead salt stabilizers are gradually being phased out due to toxicity issues, and calcium-zinc stabilizers and organic stabilizers are becoming mainstream.
RoHS and REACH compliance: Ensure that stabilizers do not contain banned substances such as cadmium, mercury or specific phenolic compounds.
Low VOC emissions: Especially in automotive cables, stabilizers with low volatile organic compounds (VOC) are preferred.
Choosing a stabilizer that complies with regulations not only avoids legal risks, but also enhances the competitiveness of your product in the green market.
4. Balancing cost and performance
Cost is another important consideration when it comes to meeting performance requirements. High-end stabilizers (e.g., organotin) offer excellent performance but are more expensive, while Ca/Zn stabilizers strike a good balance between cost and environmental friendliness. Manufacturers need to choose the right stabilizer based on budget and market positioning.
Common PVC Stabilizer Types and Their Applicability
Currently, PVC stabilizers commonly used in the wire and cable industry include the following:
1. Calcium-zinc stabilizers
Characteristics: non-toxic, environmentally friendly, RoHS and REACH compliant, good weather resistance.
Applicable scenarios: indoor and outdoor cables, especially for products with high environmental requirements, such as household wires and communication cables.
Advantages: moderate cost, stable processing performance, suitable for mass production.
Disadvantages: heat resistance is slightly inferior to lead salt or organotin stabilizers, high temperature applications need to optimize the formula.
2. Organic tin stabilizer
Characteristics: excellent thermal stability, good transparency, excellent processing performance.
Applicable scenarios: high temperature cables, transparent cables or products with very high requirements for electrical performance.
Advantages: heat resistance, suitable for complex processing technology.
Disadvantages: higher prices, some organic tin compounds may be subject to environmental regulations.
3. lead salt stabilizer
Characteristics: Excellent thermal stability and electrical properties, low cost.
Applicable scenarios: traditional low-cost cables, but has been gradually phased out in areas with strict environmental requirements.
Advantages: low price, stable performance.
Disadvantages: Containing lead is toxic and does not meet modern environmental standards.
4. Composite stabilizers
Characteristics: combining the advantages of a variety of stabilizers, flexible formulations.
Applicable scenarios: multifunctional cables, such as special cables with both high-temperature and weather-resistant requirements.
Advantages: customizable and adaptable.
Disadvantages: need to adjust the formula according to the specific needs, high R & D costs.
Recommendations for selection in practical applications
To ensure that the right PVC stabilizer is selected, here are a few practical suggestions:
Work with your supplier to test: The performance of different stabilizers in actual production may vary depending on the equipment and formulation. It is recommended to work with your supplier to conduct small-scale trial production to evaluate the stabilizer's thermal stability, processability and end-product performance.
Focus on formulation optimization: Stabilizers are often used in conjunction with other additives (e.g., lubricants, plasticizers). Optimizing formulations can improve overall performance, such as adding antioxidants to enhance weathering resistance.
Consider long-term performance: The service life of cables can be decades, and the long-term thermal stability and aging resistance of stabilizers are important considerations when making a selection.
Follow industry trends: As technology advances, new environmentally friendly stabilizers are emerging. Regularly follow industry trends to choose more competitive products.
Summarize
Choosing the right PVC stabilizer for wire and cable is a decision that requires comprehensive consideration of performance, cost, environmental protection and processing needs. By defining the application scenario for the cable, matching the processing, ensuring regulatory compliance and balancing cost, you can find the type of stabilizer that is best suited for the job. Calcium-zinc and organotin stabilizers are the dominant choices today for their environmental friendliness and performance, while compound stabilizers offer flexible solutions for specific needs.
We hope the guidelines in this article will help you make an informed decision on your PVC stabilizer selection! If you have further questions or need customized advice, please feel free to contact a specialized supplier or industry expert!